Understanding the CNC Hydraulic Press Brake
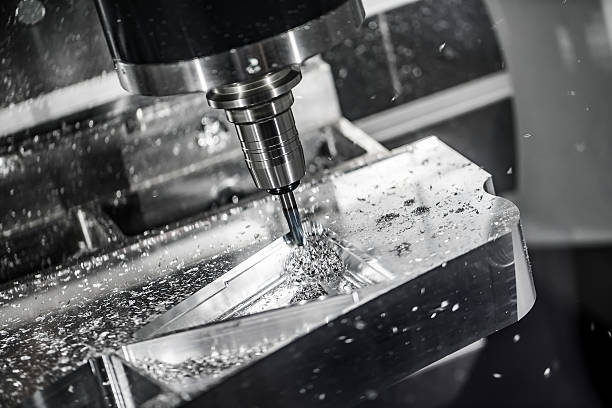
What is an CNC Hydraulic Press Brake?
CNC hydraulic press brakes are a large cold forming machine designed for precision metal forming. It is able to bend sheet metal into desired forms. Some models can deliver up to 4000 tonnes of bending force. A normal press is between 4 and 30 feet.
Design & Construction
The most important components in a CNC press brake for sale include a
hydraulic unit as well as a control panel a controller with an automatic feeder
as well as a bolster plate an ram, as well as the frame. Here we will discuss
some of the essential components.
Column and bench
The workbench is comprised of the base and the press plates. The clamping plate is attached to the workbench by an articulation hinge. The columns form part of the frame which is the foundation for all the parts that are on the machine. The workpieces are bent onto the workbench.
Press Plate
On the base is mounted the press plate, or the bolster plate. It is fitted with die cushions that permit the press brake to apply counter-draw forces. The sheet metals are fed between the bolster plate and the Ram guide during the process, which is shaped by the lower and upper dies.
Guidance for Ram/Slide
The ram is where upper dies are attached which causes the dies to press against a workpiece. The force that presses the ram is managed by the CNC system. The ram's movements are controlled by the type of drive. Solid guidance and appropriate control are essential to a long-lasting life of the hydraulic press brake.
Controller and Feeder
Generallyspeaking, computer numerical control utilize automatic feeders to consistently feed the raw materials to the area of forming. Other machines, such as the sheet metal straightener and decoiler treat the materials before they are loaded.
Working Principle
Brake shaping typically molds metals as thick as 10" thick, and certain equipment can form pieces as large as 20 feet. The bent angle may be precisely controlled through regulating the amount of the ram's movement. The ram is lowered to press against the sheet metal held by the lower die. Die set design stipulates that the sheet material will change its shape as the force is applied.
Advantages
A CNC hydraulic press brake offers many advantages due to its simple design and operating principle. They're simple to operate efficient, affordable, adaptable and efficient. Let's take a look at the advantages of this technology.
Easy to make use of
CNC press brakes are an easy and user-friendly device. They are numerically operated machines that allow even semi-skilled workers to conveniently program and rapidly make all the required components. The controller guides the operator in a sequential way, making it simple for novice operators to operate the machine.
Flexible CNC Programming
Modular programming makes it simple to set up your unit. When the right operation is selected, a second set of options (cycle time, times for bending degree, flange length and many more) relevant to the manufacturing process are displayed on the panel. After the variables are set, the values will be displayed on the screen. The machine is now set to go.
Multitasking and Energy-saving
It is a multitasking system that requires only one operator to inspect the first component and also perform work on the second component's program. Other operators can work simultaneously in other areas, such as programming. In terms of configuration, it's energy-efficient.
If the slide guide is empty, it does not use any energy. The hydraulic pumps and motor are the parts which require a constant supply of power. The CNC system guarantees the power supply is efficient. The slider allows for quick and accurate presses, further reducing the energy use.
Structural Integrity
As opposed to other forms of forming that require joining parts using heat, the press brake can do the job without heating and melting. This speeds up the process while ensuring the identical (sometimes more) quality of the part. This can significantly increase the overall productivity.
Versatility
The CNC hydraulic press brake comes in numerous shapes with the freedom to bend the sheet metals at nearly any angle you want. Additionally, it is able to process various types of metals. The CNC system allows for a wide variety of designs and bends that are unique with high precision and permits the perfect fit for many applications.
Applications
As a sheet metal forming machine CNC hydraulic press brakes often work with shearing machines, sheet angle cutting machines, and many more to create complex surface profiles of sheet metal. The CNC hydraulic press brake has an impressive forming capacity and precision and is increasingly popular across a range of industries like military, automotive, transportation, energy and aerospace.